It is common knowledge that the screw can be tapped in the threaded bottom hole of the piece to which it is connected. This is possible due to the high hardness of the thread surface as well as the fact that the thread of the stainless steel self-tapping screw is an ordinary thread with an arc-shaped triangular section. In addition, the thread of the screw has a self-tapping design. Because of this, the screw can serve both the purpose of connecting and threading when it is used. in order to get the connection going, you need to use the thread. When compared to standard self-tapping screws, the working performance of this particular variety of screw is superior because it requires less torque to screw it in and has a higher locking performance. Because of its ability to provide a higher level of locking performance, it can be used in place of machine screws in a variety of applications.
If that's the case, what are some of the characteristics that self-tapping screws made of stainless steel have?
1. Wallboard self-tapping screws are used to secure the connection between gypsum wallboard and other types of wallboard as well as metal joists. The surface of the thread has a high degree of hardness (approximately HRC53), and the thread cheese head screws itself is double-headed. Because of this, the connection can be easily screwed into the keel without the need to first make a hole in the keel that has been prefabricated.
2. In circumstances in which it is acceptable to expose the drill bit, using self-tapping screws made of stainless steel with either a pan head or a hexagon head is an option that is suitable for the job at hand. The amount of torque that can be applied by self-tapping screws with hexagon heads is typically higher than the amount of torque that can be applied by self-tapping screws with pan heads. Countersunk head self-tapping screws and hexagon socket self-tapping screws are two options that should be considered for use in situations in which it is undesirable for the nail head to be visible. Self-tapping screws that have a hexagon socket are able to withstand a greater torque than self-tapping screws that have a flat head because the hexagon socket provides more surface area. The use of self-tapping screws that have a head that is only partially submerged is recommended for applications in which the screw heads will be partially visible. When it comes to installing and disassembling self-tapping screws, slotted self-tapping screws require a screwdriver with a flat blade, cross-recessed self-tapping screws require a screwdriver with a cross-shaped head, hexagon socket self-tapping screws require a socket wrench, and hexagonal head self-tapping screws require a hexagonal head screwdriver. Other types of self-tapping screws require a screwdriver with a cross-shapedTo tap screws, you will need a flat wrench, a Torx wrench, a socket wrench, or an adjustable wrench. You can also use an adjustable wrench.3. Ordinary screws that are self-tapping must go through two processes in order to be connected: drilling (drilling threaded bottom holes) and tapping (including fastening connections). This is not the case with self-tapping screws made of stainless steel; in order to connect them, only one step is necessary. The drilling and tapping processes are combined into a single unified operation once the tapping screw is connected. This allows the processes to be performed simultaneously. It begins by drilling with the drill bit in front of the screw, and then it uses the screw for tapping (including the connection for the fastening), which saves time during the construction process and improves the overall efficiency of the construction industry as a whole.
Self-tapping screws are screws that, when screwed into materials such as wood, plastic, or metal, create their own holes in the material for the fasteners to go through. When connecting self-tapping screws, you can create threads that are a precise fit for the application by using a screwdriver. They are an excellent choice for joining together two different kinds of material, as well as for screwing into areas that can only be reached from one side. Additionally, they are an excellent choice for joining together two different kinds of material. For products that require routine maintenance (like air conditioning Heatfastener units or canopies), it can be helpful to use self-tapping screws when you need to disassemble and reassemble items along the same threads. This can be done with the use of self-tapping screws. When you need to take things apart and put them back together again, you are in this situation.
Self-tapping screws have the capability of either cutting or forming their own threads, and both of these processes are referred to as self-tapping. When working with plastics, thread forming screws are utilized so that the material can be deformed as the screw is inserted. This allows for greater precision when working with the material. Even though thread-forming screws are held in the material more securely, there is still the possibility of overtightening the screw, which can result in the material cracking as a result of the pressure. This is because the screw is applying more force to the material than it was designed to handle. On the other hand, thread cutting screws are typically utilized on wood and metal, and their purpose is to literally remove some material while simultaneously creating a thread path for the screw. This is accomplished by cutting a path through the material for the threads of the screw. The threads on thread-cutting screws have a propensity to flake off when the screw is removed, which is one of the most significant disadvantages associated with the screws. In the event that this occurs, you will want to make sure that the product is reassembled using self-tapping screws that have a diameter that is slightly larger.
When it comes to preventing peeling over the long term, one of the most effective strategies tamper proof screws is to incorporate metal inserts into the material from the very beginning. After that, you won't run the risk of damaging the material if you use screws of the appropriate size to regularly adjust how tightly the connection is made or how loosely it is made. The configuration of the blades is designed to reduce stress to the greatest extent possible, and as the screw moves forward, the blades lengthen.
The heads of self-tapping screws can take on a variety of shapes and sizes, and there is a wide variety of sizes and types of tips available for use with these screws. Self-tapping screws are very versatile. When choosing the right size of self-tapping screw, it is essential to take into account the thickness of the material in order to determine the length of the screw tip. This can be done by multiplying the thickness of the material by the size of the screw. Before beginning the process of threading, there needs to be enough room for the point of the drill screw to completely enter the material that is being worked on. This must be accomplished before the process can begin. In the event that this does not take place, the threads on the final product will be damaged as a result of the screw being inserted, and it will not be possible to secure it in the correct manner.
There are two distinct types of self-tapping screws which are known as thread forming screws and thread cutting screws
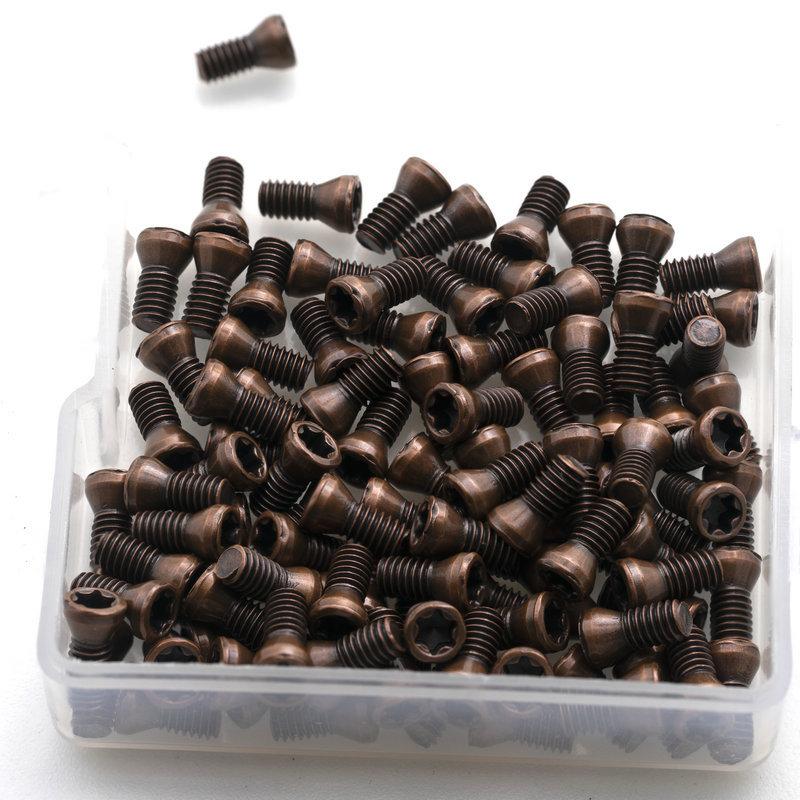
Read More
(%<18>%)X.X.X@VIDEOS]* Indian Teen School Girl sot
CLICK THIS L!NKK